Vacuum Forming vs. Lamination: Best Practices for High-Precision Ceramics
High-precision ceramics are pivotal in industries where exact specifications are key, like electronics, aerospace, and medical devices. This means that shaping these ceramics often involves advanced techniques that can produce components with the required accuracy and properties; two of these methods are vacuum forming and lamination.
While each technique offers its own advantages, there are times when one may be the best choice. Let Smartech walk you through the benefits, drawbacks, and applications of each method.
Vacuum Forming
Vacuum forming is a widely adopted method for creating ceramic parts, used primarily when intricate details and uniform thickness are necessary. The process involves heating a sheet of ceramic material until it becomes pliable and then using a vacuum to pull the material tightly over a mold. As the material cools, it retains the shape of the mold, resulting in a precise and consistent ceramic part.
This vacuum forming process is highly regarded for its ability to produce complex shapes with remarkable accuracy. It is particularly cost-effective for small to medium production runs, making it a preferred choice for manufacturers who need to balance precision with budget constraints. By using precise molds and controlled vacuum pressure, vacuum forming can achieve exceptional detail in the final product. However, it is essential to manage the heating and cooling cycles properly to avoid thermal stress and cracking, which could compromise the integrity of the ceramic.
However, very thick or large ceramic parts may not form as easily, and there can be challenges related to material waste during trimming processes.
Lamination in Ceramics
Lamination is another popular technique for manufacturing high-precision ceramics. This process involves stacking multiple layers of ceramic materials and bonding them together using heat, pressure, or adhesives. The lamination technique is highly effective for creating multilayered components that require specific dielectric properties or enhanced structural integrity.
Lamination is particularly beneficial for applications that demand high strength and durability. By layering ceramic materials, manufacturers can produce components that are not only robust but also customizable in terms of their electrical properties. This makes lamination an excellent choice for creating electronic components, sensors, and other devices that require precise performance under various conditions.
However, lamination is often more labor-intensive and time-consuming than vacuum forming. The process requires careful control of each layer’s thickness and bonding quality to ensure a uniform and high-quality final product. Additionally, lamination can be more costly for smaller production runs due to the additional labor and materials required.
Key Differences: Vacuum Forming and Lamination
When deciding between vacuum forming and lamination, you should understand the key differences between the two processes. Vacuum forming is generally more suitable for simpler, uniform shapes and is highly cost-effective for low to medium production volumes. Its ability to produce intricate designs with consistent thickness and minimal material waste makes it a popular choice for various ceramic components, such as medical device parts, insulators, and casings.
On the other hand, lamination is better suited for more complex, multilayered designs that require additional strength or specific electrical properties. It is ideal for applications involving multilayered circuit boards, sensors, and electronic components. While it may involve higher costs and more labor, lamination offers unmatched benefits in terms of strength, durability, and customization.
The choice between these two methods often comes down to factors like design complexity, production volume, material characteristics, and overall cost. Different types of ceramics, such as alumina or zirconia, may respond differently to these processes, and understanding these nuances is critical for achieving the best results.
Best Practices for Vacuum Forming
To achieve optimal results with vacuum forming for ceramics, Smartech recommends:
- Uniform Heating and Cooling: Proper thermal management prevents stress and cracking in ceramics.
- Precision Molds and Controlled Vacuum Pressure: Accurate molds and vacuum control ensure precise details.
- Efficient Material Management: Minimizing material waste through optimized trimming and recycling is essential.
Ideal Applications: Vacuum forming works best for medical devices, insulators, and casings that require precision and uniformity.
Best Practices for Lamination
For effective lamination of high-precision ceramics:
- Selecting the Right Bonding Agents: The choice of adhesive affects the strength and properties of the final product.
- Controlling Layer Thickness: Ensuring consistent layer thickness is crucial for uniformity in properties.
- Clean and Controlled Environment: Maintaining a clean setting prevents contamination and ensures product integrity.
- Ideal Applications: Lamination is perfect for multilayered circuit boards, sensors, and components that need specific electrical properties.
Quality Matters: Trust Smartech for Reusable Vacuum Bags
When it comes to high-precision ceramics, selecting the right shaping method is crucial for achieving the desired quality and performance.
If vacuum forming is right for your project, Smartech offers a range of high-quality, reusable vacuum bags designed to enhance the efficiency and precision of this process. These reusable vacuum bags are crafted to provide superior performance, reducing material waste and optimizing production for the best results possible!
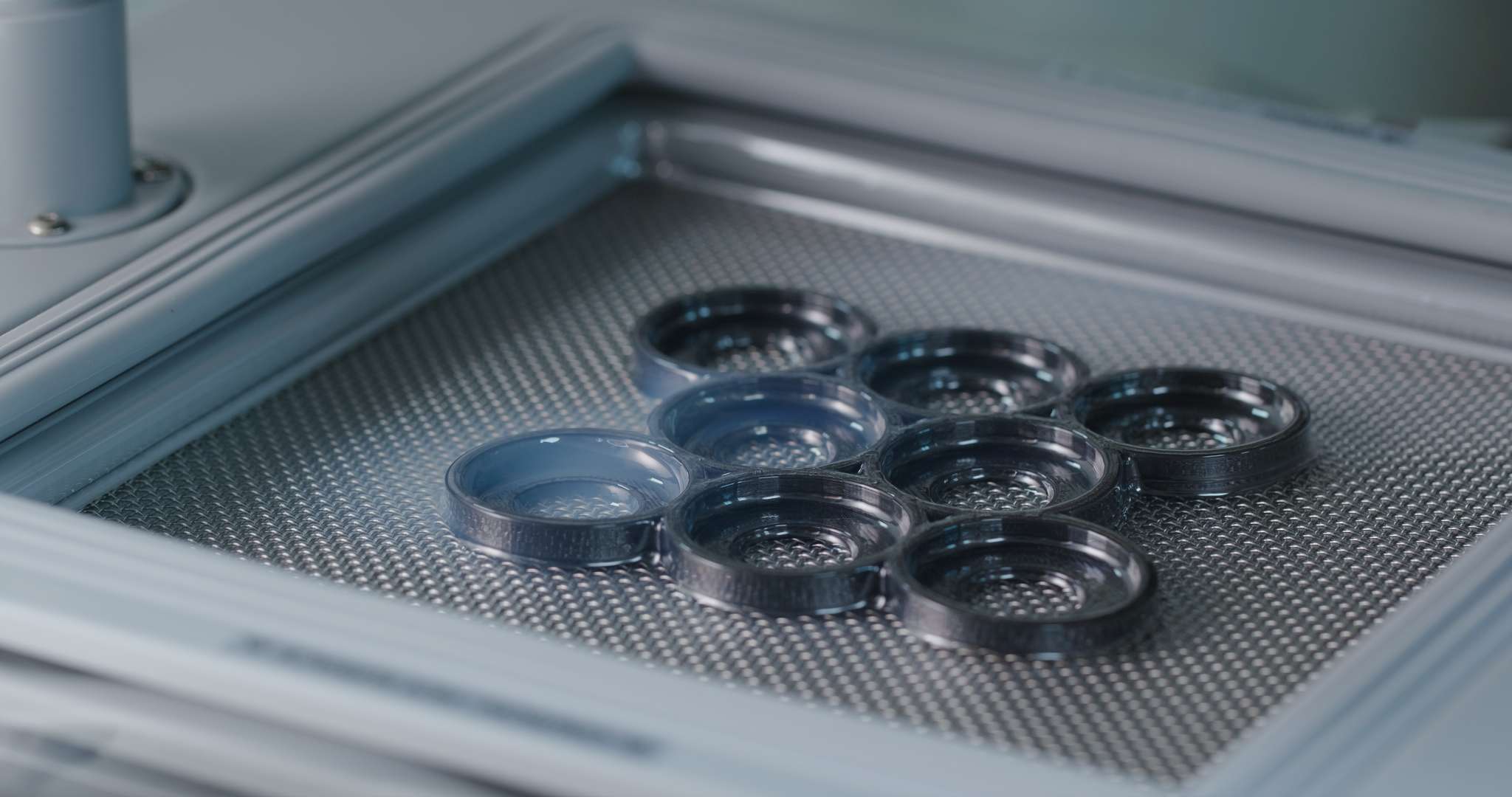
Looking for More Information?
Check out our Resources or Contact Us