Custom 3D Printed Ceramic Components
In partnership with Steinbach’s Technical Ceramics department, we can create highly precise ceramic components. This could be for prototypes as well as series production.
The ceramic parts are lightweight and heat-resistant. Your parts will be created through our process called the Lithography based ceramic manufacturing method (LCM). The main advantage of LCM over conventional 3D printing is the incredible precision that can be achieved.
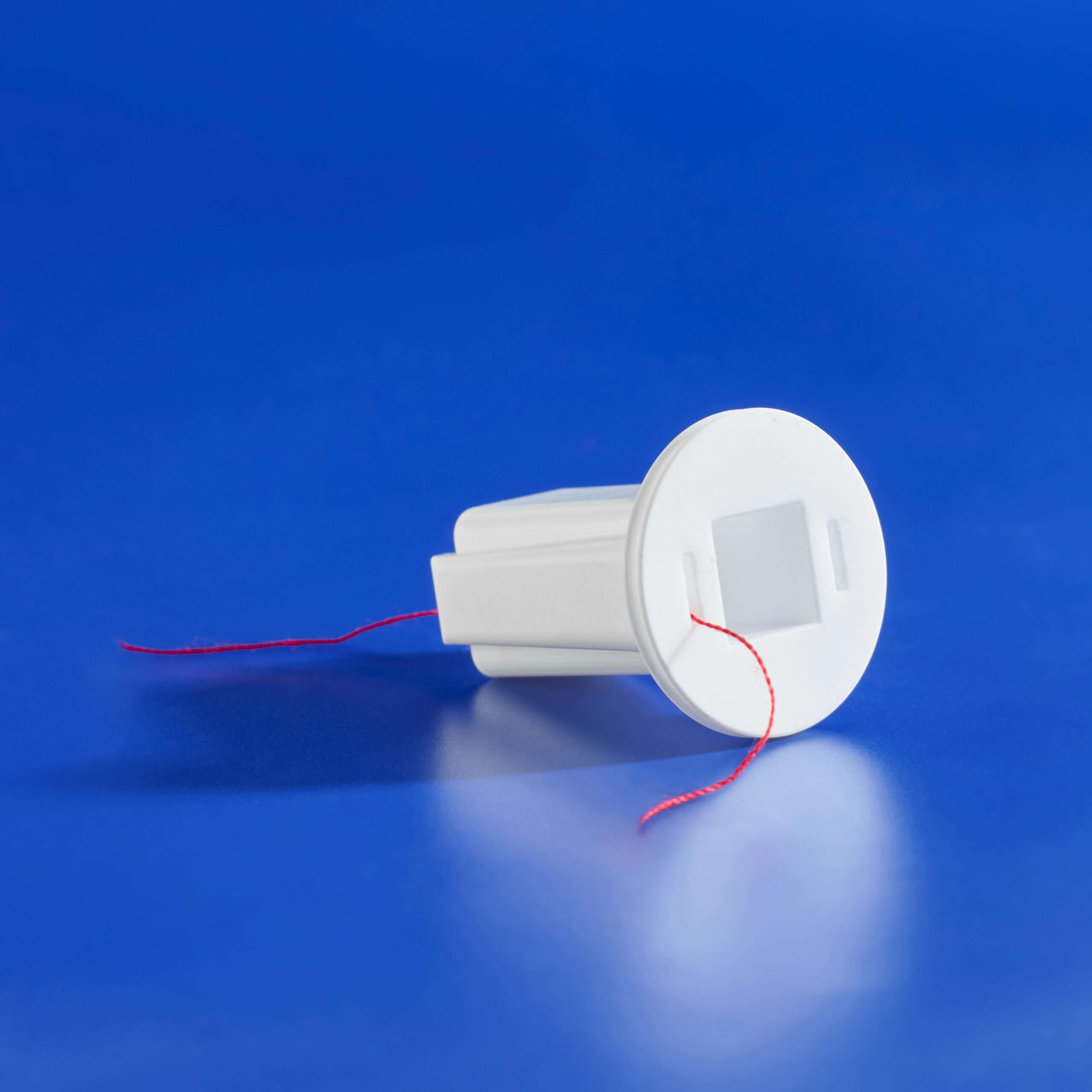
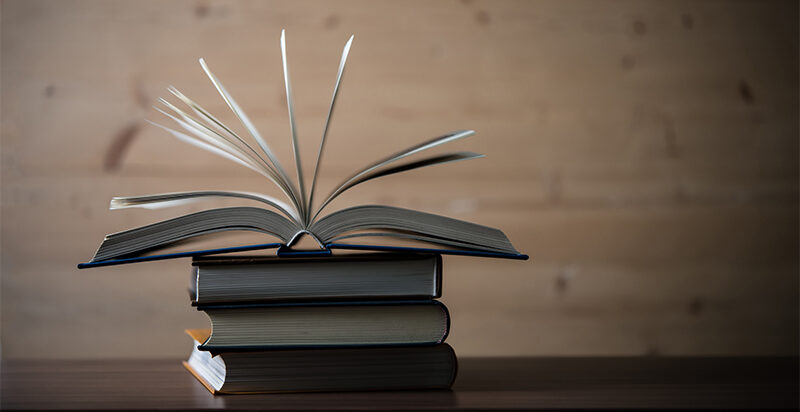
Did you know that LCM ceramic parts are:
- heat-resistant up to 1600°C/2900°F
- non-conductive
- wear-resistant
- smooth surface
- biocompatible
- solid
- food safe
- chemically resistant.
The ceramic parts that Steinbach creates with Additive Manufacturing are used in:
- Medical technology
- Automobile industry
- Analysis and measurement equipment
- Microreactors / Microfluidic applications
- Micro-electronics
- Plasma technology
- High-temperature application
- Aerospace sector
- Chemistry and laboratories
LCM allows state-of-the-art design freedom to develop components.
It allows to design parts that cannot be manufactured by conventional methods on this level of high quality. LCM consist of 7 steps:
1: It all starts with a CAD model of the design (STEP-file)
2: Then you need to choose the material; Aluminum oxide Al2O3 or Zirconium oxide (zirconia) ZrO2
3: The LCM (actual printing) process
4: Cleaning of the greenlings
5: De-binding, removing the polymer
6: Sintering: consolidation of the ceramic particles.
7: Quality Control
FAQ'S
What are the advantages of ceramics over plastics?
The biggest advantage of ceramic parts is that they are heat-resistant up to 1600°C/2900°F. But there are other reasons why developers chose ceramic over plastic/polymer parts. Ceramic parts are non-conductive, wear-resistant, have a smooth surface, are biocompatible, food safe and chemically resistant.
Is ceramic more environmentally friendly than plastic?
Yes, Ceramic is friendly to the environment. It is a mixture of earth minerals, clay, and water. On the other hand, plastics/polymers are man-made synthetic products that take a long time to break down.
Is ceramic a better insulator than plastic?
The thermal conductivity of ceramic parts depends on several factors such as the kind of ceramic material, for instance Aluminum oxide or Zirconium oxide, the purity and density. But in general, ceramic parts have much higher insulating properties than plastics/polymers.
Which polymer/plastic can withstand high temperatures?
Not all plastics/polymers will melt. But even thermoset polymer/plastic should not be exposed to high heat. Ceramic parts are a great alternative to polymers when exposed to high heat.
Is it cheaper to injection mold or 3D print?
3D printing doesn’t need any tooling other than the printer. Therefore, the non-recurring engineering (NRE) costs are very low. Changes in design during the developing/proto-typing process can be made by just changing the STEP.file drawing. In the last few years, ceramic 3D printin
How precise is a ceramic 3D printer?
The accuracy in processing ceramic parts by using the Lithography Ceramic Manufacturing (LMC) process, is mainly determined by the shrinkage in the thermal process. The following tolerances apply: ± 1 % of the linear measure but maximum ± 0.1 mm. Depending on the geometry higher accuracy can be achieved by iterative approximation.
How much does a 3D ceramic printer cost?
Professional Industrial ceramic 3D printers may cost more than half a million dollars. In addition, you will need de-binding and sintering ovens. There are companies like Smartech/Steinbach who have the
What is additive manufacturing?
Additive manufacturing means that a product is created by adding thin layers. 3D ceramic printers are an example of the additive manufacturing process.
Can a ceramic 3D printer be used for mass production?
Smartech/Steinbach developed and produced a ceramic part for a well-known medical device manufacturer in a series production of more than 12,000 units per year.
Looking for More Information?
Check out our Resources or Contact Us