Vacuum Bagging Process & Equipment for Composites
In the realm of composite manufacturing, achieving high-quality and consistent results is crucial. One method that ensures this is vacuum bagging, a technique used to create strong, durable, and lightweight composite materials. So, what is vacuum bagging, and why is it relevant?
Vacuum bagging is a process where layers of composite material, usually a reinforcement fabric and a resin, are placed in a mold and then sealed in an airtight vacuum bag. This bag is then evacuated of air, applying uniform pressure on the layers, ensuring optimal compaction and curing. This method is essential for creating composites that are free of voids and imperfections, ensuring an even and thorough cure.
The Science Behind Vacuum Bagging
The science behind vacuum bagging lies in the principle of atmospheric pressure. When the air is evacuated from the vacuum bag, the atmospheric pressure outside the bag pushes against the layers of composite materials, applying uniform pressure across the entire surface. This pressure ensures that the resin thoroughly wets out the reinforcement and that there are no trapped air pockets or voids within the laminate.
By effectively manipulating atmospheric pressure, vacuum bagging facilitates an environment where the resin can flow more freely into the fibers of the reinforcement, ensuring a higher fiber-to-resin ratio. The result is a composite material that is both stronger and lighter than what could be achieved through manual layering alone.
Equipment Required for Vacuum Bagging
Vacuum Source: A reliable vacuum source is the powerhouse of the vacuum bagging process. Vacuum pumps, whether they are piston, rotary vane, turbine, diaphragm, or Venturi types, are commonly used. These pumps come with ratings that indicate their maximum vacuum pressure and air-moving capacity. The ideal pump for a vacuum bagging operation would have the largest air-moving capacity for the required vacuum pressure while operating at a reasonable horsepower.
Bagging Film: Bagging film forms the envelope that contains the composite layers. Made from materials like nylon or polyethylene, it is crucial to choose one that is robust and airtight.
Sealant Tape and Peel Ply: Sealant tape plays a crucial role in ensuring an airtight seal around the vacuum bag, preventing air leaks. On the other hand, peel ply is placed directly on the wet laminate, providing a textured finish when removed and reducing the need for surface prep before secondary bonding.
Breather Fabric and Release Agents: Breather fabric, also known as a ‘baby blanket’, serves two main purposes. It absorbs excess epoxy squeezed out from the laminate, and it allows air to be evacuated from the compacted laminate due to its open structure. Release agents, on the other hand, prevent the epoxy from sticking to the mold, ensuring an easy de-molding process once the epoxy has cured.
Miscellaneous Tools: Other tools required for vacuum bagging include scissors for cutting materials, gauges for measuring vacuum pressure, connectors for attaching vacuum lines, and hoses for creating an airtight passage from the envelope to the vacuum pump.
Step-by-Step Guide to the Vacuum Bagging Process
Understanding the vacuum bagging process is essential for producing strong, lightweight composite materials with minimal imperfections.
- Preparation: The process begins with cleaning and preparing the mold. A release agent is applied to prevent the composite material from sticking during curing.
- Laying the Reinforcement: The reinforcement material, such as fiberglass or carbon fiber, is laid on the mold and wetted with resin, ensuring a precise fit and thorough coverage.
- Peel Ply and Release Film Application: The peel ply is applied over the wet reinforcement, followed by the release film. These layers facilitate easy removal of the vacuum bag and provide pathways for excess resin to escape.
- Breather Cloth Placement: A breather cloth is placed over the release film, serving to distribute vacuum pressure evenly and absorb excess resin.
- Sealing in Vacuum Bag: The layered mold is enclosed in a vacuum bag, ensuring a wrinkle-free and airtight seal with sealant tape, leaving an attachment spot for the vacuum hose.
- Evacuation: The vacuum pump is activated, evacuating air from the bag and compressing it onto the mold, with constant vacuum level monitored using a gauge.
- Curing: The composite is left to cure under vacuum, with the duration varying based on the resin system used. Some systems may require heat application during curing.
- Demolding: After curing, the vacuum pump is switched off, and the bag, breather cloth, release film, and peel ply are carefully removed, revealing the composite material which is then separated from the mold.
- Inspection and Finishing: The final composite part is inspected for flaws, trimmed, and potentially sanded or finished to achieve the desired appearance and texture.
By diligently following these steps, the vacuum bagging process can yield high-quality composite parts suitable for a wide range of applications.
Introducing Reusable Vacuum Bagging Solutions: A Game-Changer in Composite Manufacturing
The vacuum bagging process, while highly effective, has traditionally been seen as consuming both time and resources. However, the advent of reusable vacuum bagging solutions is revolutionizing the landscape of composite manufacturing. These innovative solutions are significantly more cost-effective and efficient compared to single-use bags, making them a game-changer in the industry.
Reusable vacuum bagging brings several compelling advantages to the table:
- Cost-Efficiency: With the ability to be used multiple times, these bags reduce the overall cost per unit of production.
- Time-Saving: The elimination of pleating reduces the time taken for setup, allowing for quicker project turnovers.
- Resource Optimization: There’s a substantial reduction in waste products, aligning with eco-friendly practices.
- Labor Savings: The ease of use means that less skilled labor is required, saving on labor costs.
- Consistency and Complexity: The process ensures increased consistency in parts and can accommodate complex shapes and designs.
Read more about the benefits of reusable vacuum bagging
Reusable Vacuum Bagging Solutions with Smartech
Smartech, in partnership with Steinbach, presents cutting-edge reusable vacuum bagging solutions designed to elevate your manufacturing processes. These innovative solutions are meticulously crafted to ensure reduced costs, minimal expendables, significant labor savings, and consistent high-quality outputs. Steinbach’s reusable bags are tailored to your specifications, offering versatility with options in durometers, valve fittings, and surface textures.
From facilitating complex part production to ensuring a smooth workflow, Smartech’s solutions redefine composite manufacturing.
Discover the transformative power of Steinbach’s reusable vacuum bagging with Smartech’s diverse solutions. Elevate your production line by exploring our product specs and contacting Smartech today.
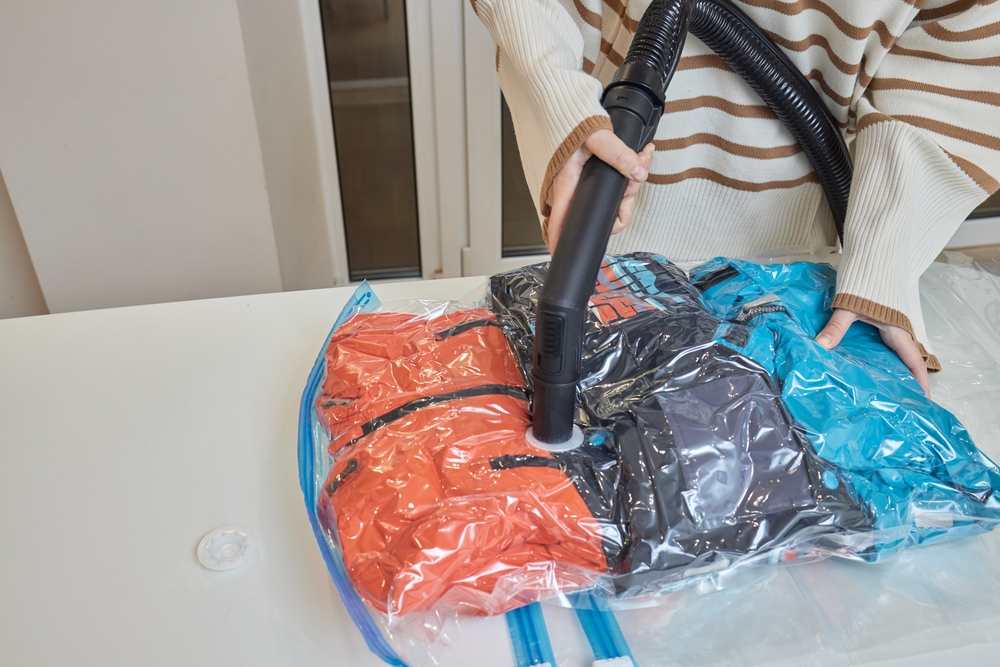
Looking for More Information?
Check out our Resources or Contact Us