Vacuum Bagging Carbon Fiber: Process & Equipment
Vacuum bagging, a pivotal technique in carbon fiber manufacturing, stands as a testament to the evolution of material technology. This process not only streamlines production but also enhances the quality of the final product. It’s a game-changer in achieving superior composites, crucial in applications where strength and precision are paramount.
The Basics of Vacuum Bagging in Carbon Fiber Fabrication
Vacuum bagging is a sophisticated process used in carbon fiber production to create materials that are lighter, stronger, and more durable than their counterparts. At its core, vacuum bagging carbon fiber parts involves placing the carbon fiber material inside a vacuum bag and extracting the air. This vacuum pressure compacts the fibers tightly against the mold, ensuring that the resin distributes evenly and minimizes voids.
Essential Equipment for Vacuum Bagging Carbon Fiber
The right equipment is the linchpin of successful vacuum bagging. Key components include:
- Vacuum Pumps: The heart of the operation, ensuring a consistent and strong vacuum pressure.
- Bagging Film: A durable, flexible material that conforms to the mold and the material.
- Sealant Tape: Ensures airtight seals at all connection points to maintain vacuum integrity.
- Peel Ply & Release Films: Facilitate easier removal of the bagging materials and smooth finish.
Selecting the right equipment is not a one-size-fits-all situation. Factors such as project scale, complexity, and specific material properties must guide your choices. For smaller projects, a simpler setup might suffice, while larger, more complex tasks may require advanced systems with higher capacity and control.
Step-by-Step Process of Vacuum Bagging Carbon Fiber
Achieving perfection in vacuum bagging carbon fiber requires precision and patience. Here’s a detailed guide on how to vacuum bag carbon fiber parts:
- Preparation: Cut and lay the carbon fiber material over the mold. Ensure the work area is clean and all materials are readily accessible.
- Applying Release Agent: Apply a release agent to the mold to prevent sticking.
- Laying the Carbon Fiber: Carefully place the carbon fiber layers onto the mold, ensuring there are no wrinkles or misalignments.
- Applying Epoxy Resin: Brush or spray the resin over the carbon fiber layers, ensuring even coverage.
- Placing Peel Ply & Release Film: Apply these layers to facilitate the vacuum process and achieve a smooth finish.
- Bagging: Cover the layup with the bagging film and seal all edges with sealant tape.
- Vacuuming: Attach the vacuum pump and extract the air to compact the material against the mold.
- Curing: Allow the material to cure under vacuum pressure for the required time.
- Finishing: Once cured, remove the vacuum bagging materials and release the finished product from the mold.
Advantages of Vacuum Bagging in Composite Material Production
Vacuum bagging significantly improves the quality and durability of carbon fiber composites, offering clear, practical benefits:
- Enhanced Mechanical Properties: It increases the fiber-to-resin ratio, which results in higher tensile strength and stiffness.
- Improved Aesthetics: The process eliminates air bubbles and defects for a smoother finish.
- Reduced Material Waste: Better resin control leads to less waste, making it cost-effective and environmentally friendly.
- Consistent Quality: The controlled environment ensures reliable, repeatable results, critical in high-performance applications.
In industries like aerospace and automotive racing, vacuum bagging is crucial for producing components that are both lighter and stronger, demonstrating its effectiveness in real-world scenarios.
Smartech’s Role in Revolutionizing Vacuum Bagging
Smartech is changing the game in the composite industry with its Reusable Vacuum Bagging solutions. These innovative solutions bring several key advantages:
- Tailored Solutions: Smartech works closely with clients to determine the best bagging material and method for specific product sizes and processes, ensuring maximum performance and efficiency.
- Quality Material Selection: The quality of bagging material is crucial for achieving uniform resin distribution, consolidation, and void elimination in parts. Smartech offers a wide variety of materials to suit different job requirements.
- Advanced Bag Features: Smartech’s bags are designed to be strong enough to create a vacuum, flexible enough to mold to the part, and capable of maintaining these properties under high temperatures. They are crafted from high-strength silicone materials that can withstand up to 400 degrees Fahrenheit and are customizable to specific industrial applications.
- Cost and Resource Efficiency: The reusable nature of these bags leads to reduced costs, fewer expendable materials, and waste products, as well as labor savings. Smartech provides options like vertically or horizontally oriented vacuum valves and thermo-couple pass-through fittings, catering to the specific requirements of different applications.
For professionals in composite manufacturing, Smartech’s technology represents a significant advancement in enhancing product quality and operational efficiency. The company’s focus on tailored solutions, material quality, and advanced bag features make its Reusable Vacuum Bagging solutions a valuable addition to any fabrication process.
Conclusion: Embracing Innovation in Carbon Fiber Fabrication with Smartech
The importance of vacuum bagging in carbon fiber manufacturing cannot be overstated. This process is essential for producing materials that are lighter, stronger, and more durable. Smartech’s innovative approach to offering reusable vacuum bagging solutions has revolutionized this process. Their technology not only maintains the quality and integrity of the composites but also adds an element of sustainability by reducing waste.
Contact Smartech today to explore how Smartech’s Reusable Vacuum Bagging solutions can fit into your operations and drive your projects forward,
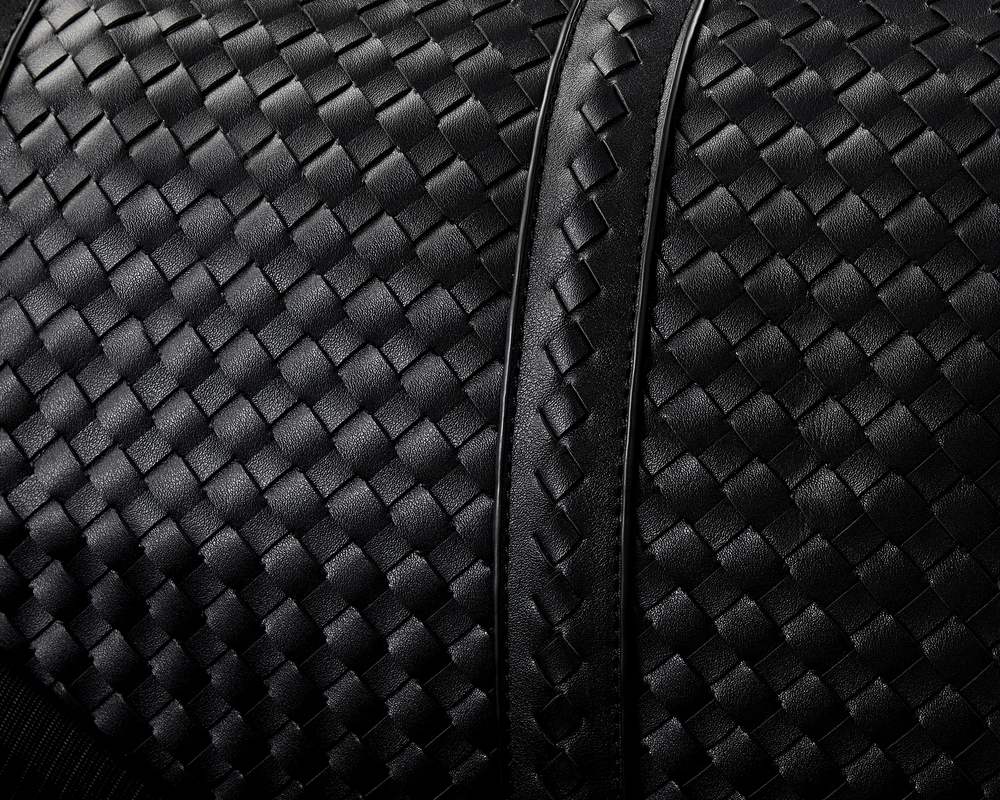
Looking for More Information?
Check out our Resources or Contact Us