Silicone Membranes vs. Traditional Vacuum Press Materials
When it comes to vacuum pressing, the material you choose for the membrane can significantly impact the quality, efficiency, and longevity of your process. Traditional vacuum press materials like latex and polyurethane have been staples in the industry for years, but silicone membranes are rapidly gaining popularity due to their superior performance and versatility. This blog explores the differences between silicone membranes and traditional materials, helping you decide which option is best for your needs.
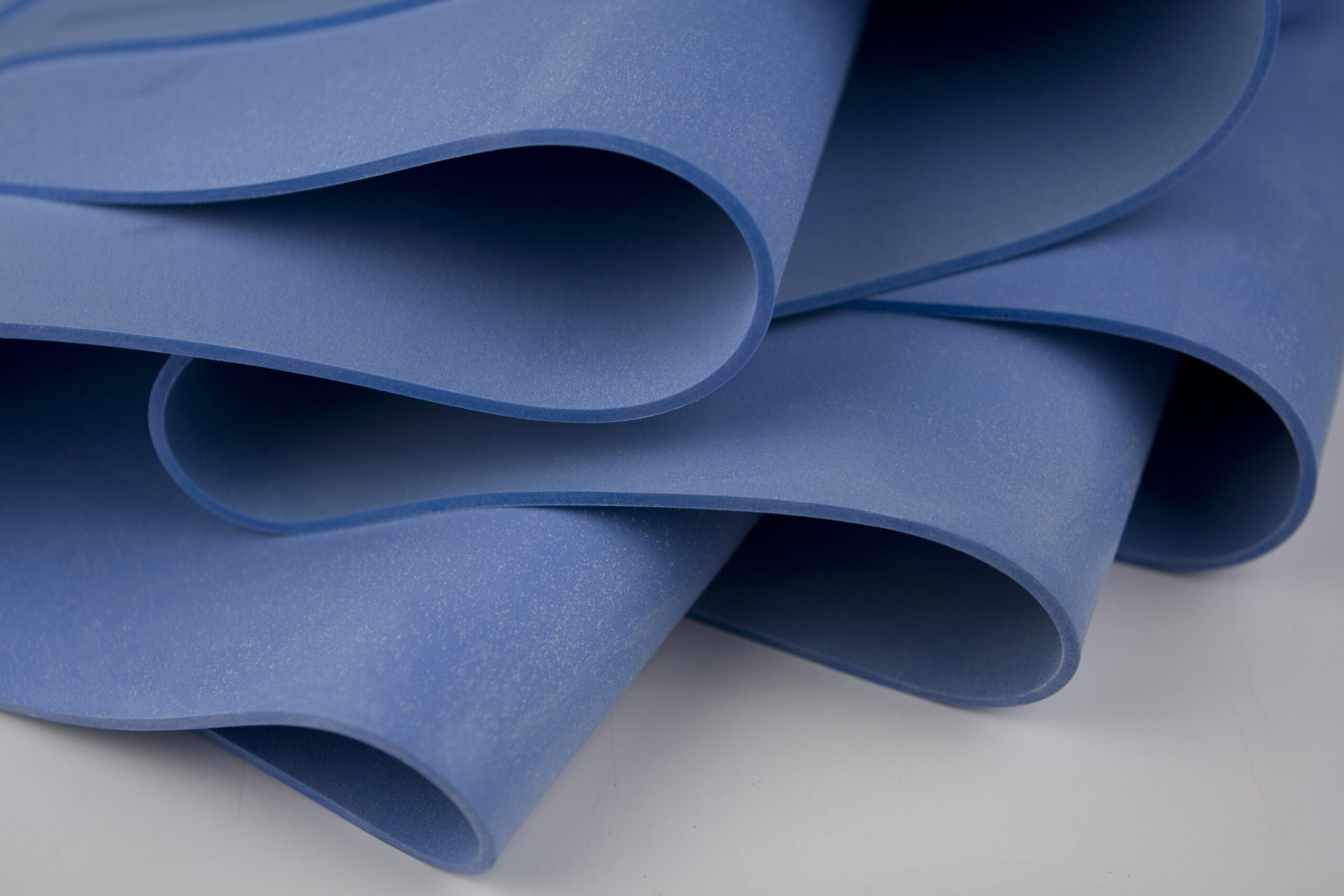
Why Membrane Materials Matter
Vacuum pressing is a versatile process used in various industries, including woodworking, thermoforming, and composite manufacturing. The membrane is a critical component, as it creates a sealed environment for applying consistent pressure to the material being processed. The durability, flexibility, and resistance of the membrane affect the overall performance and outcomes of the vacuum press.
Silicone Membranes: A Modern Solution to Old Problems
Silicone membranes have revolutionized vacuum pressing by offering a range of benefits that traditional materials struggle to match. One of the key advantages is their exceptional heat resistance. Silicone membranes can withstand temperatures as high as 230°C (446°F) or more, making them suitable for applications involving high heat, such as thermoforming or composite curing.
Another standout feature is their durability. Silicone membranes are highly resistant to wear and tear, lasting significantly longer than latex or polyurethane. This longevity reduces replacement frequency and lowers operating costs over time. Additionally, silicone’s inherent chemical resistance ensures it remains unaffected by oils, solvents, and other chemicals commonly used in industrial processes.
Silicone membranes also excel in flexibility and elasticity. They can stretch to accommodate complex shapes and intricate designs without losing their structural integrity. This makes them ideal for woodworking projects with curves or details that require precise molding.
How Silicone Membranes Compare to Traditional Materials
When deciding between silicone membranes and traditional options, it’s essential to consider several factors that influence performance and cost-efficiency. Here are key comparison points:
Durability and Longevity
- Silicone Membranes are designed to withstand repeated use, high pressures, and extreme conditions without tearing or degrading. They have a significantly longer lifespan, reducing replacement frequency and downtime.
- Latex Membranes are more prone to degradation over time, especially in high-temperature or chemically harsh environments. Frequent replacements may be necessary.
- Polyurethane Membranes can offer better durability than latex but cannot match the resilience of silicone in demanding applications.
Heat Resistance
- Silicone Membranes can withstand extreme temperatures, up to 230°C (446°F) or more, making them ideal for high-heat applications like thermoforming and composite curing.
- Latex Membranes have limited heat tolerance and are prone to deterioration when exposed to high temperatures, restricting their use to low-temperature processes.
- Polyurethane Membranes show moderate heat resistance, typically up to 120°C (248°F), but unsuitable for applications requiring extreme thermal stability.
Flexibility and Elasticity
- Silicone Membranes are highly elastic and capable of conforming to complex shapes and detailed molds without compromising structural integrity. Perfect for intricate woodworking and thermoforming projects.
- Latex Membranes are also very elastic, making them suitable for detailed work, but their lack of durability limits their overall usefulness.
- Polyurethane Membranes can be less flexible than both silicone and latex, which may restrict their use in applications requiring precise molding or irregular shapes.
Chemical Resistance
- Silicone Membranes are known to be resistant to oils, solvents, and harsh chemicals, making them suitable for chemically intensive environments like composite manufacturing and industrial lamination.
- Latex Membranes are vulnerable to chemical degradation, particularly when exposed to solvents or cleaning agents.
- Polyurethane Membranes offer moderate chemical resistance but can deteriorate under prolonged exposure to harsh substances.
Cost and Value
- Silicone Membranes have a higher upfront cost but greater long-term value due to their durability, heat resistance, and reduced need for replacements.
- Latex Membranes do have lower initial costs, but frequent replacements and maintenance add up over time.
- Polyurethane Membranes are moderate in initial cost, with a lifespan and performance level that sits between latex and silicone.
The Case for Silicone Membranes
When choosing a membrane for vacuum pressing, the decision ultimately comes down to your specific needs and priorities. Silicone membranes offer unmatched durability, heat resistance, flexibility, and long-term value, making them the superior choice for demanding applications. Traditional materials like latex and polyurethane may still be suitable for specific, less-intensive uses, but they cannot match the performance and versatility of silicone.
For businesses seeking reliable, efficient solutions for vacuum pressing, silicone membranes provide a modern and highly effective option.
Looking for More Information?
Check out our Resources or Contact Us