In industries where precision, durability, and aesthetics matter most, glass lamination has become a vital process. Whether used for architectural projects, automotive applications, or safety glass, the quality of the lamination directly impacts the end product’s performance. One material that has revolutionized this process is the silicone membrane. The introduction of silicone membrane glass lamination has elevated the standards for clarity, strength, and reliability – let’s dive in to why.
In glass lamination, layers of glass are bonded via an interlayer, usually made of polyvinyl butyral (PVB) or ethylene-vinyl acetate (EVA). The goal is to create a single, durable pane that maintains the visual clarity of the glass while adding strength and safety features. Laminated glass can be used in various applications, including windows, skylights, windshields, and decorative glass.
The success of this lamination process depends on achieving uniform pressure and heat application, which ensures that the interlayer bonds seamlessly with the glass. This is where silicone membranes play a critical role.
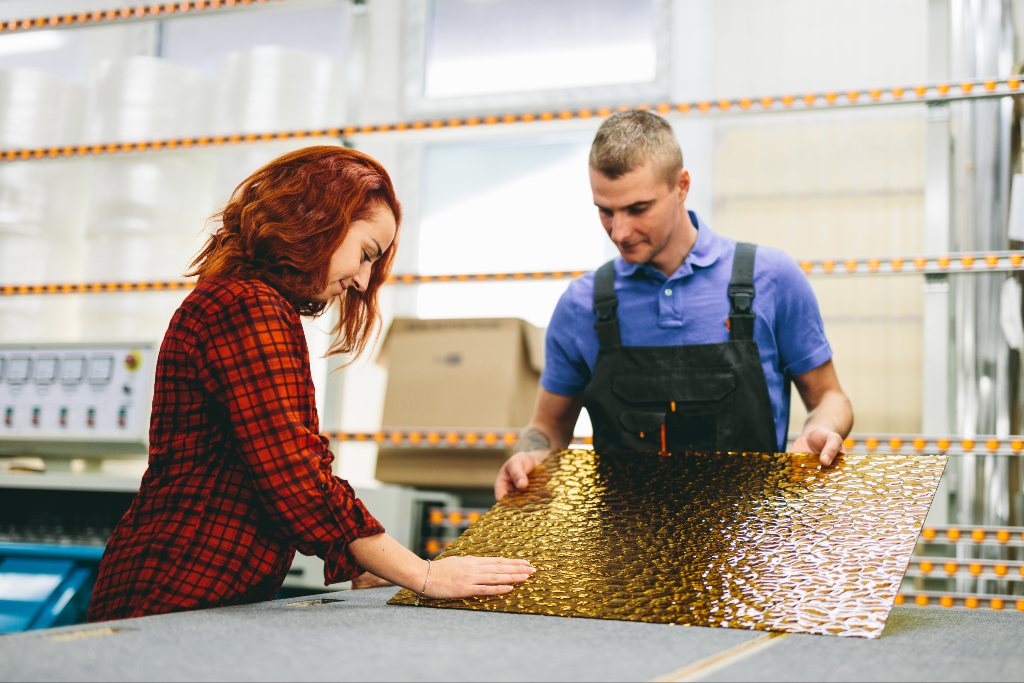
The Role of Silicone Membranes in Glass Lamination
Silicone membranes act as a flexible, heat-resistant barrier between the glass layers and the vacuum press. Their unique properties make them ideal for achieving consistent pressure distribution and optimal heat transfer during the lamination process. Here’s how silicone membranes improve the quality of laminated glass:
1. Pressure Distribution
Achieving uniform pressure across the entire surface of the glass is crucial for avoiding defects such as bubbles, wrinkles, or incomplete bonding. Silicone membranes excel in this area due to their elasticity and flexibility. They conform to the contours of the glass and interlayer, ensuring that pressure is evenly distributed, even on uneven surfaces or curved glass.
Uniform pressure eliminates air pockets and creates a flawless bond between the layers for a higher-quality finished product.
2. Heat Resistance for Consistent Bonding
Glass lamination requires precise temperature control to activate the adhesive properties of the interlayer material. Silicone membranes are highly heat-resistant and capable of withstanding the elevated temperatures required for lamination without degrading or losing elasticity.
Their ability to maintain structural integrity under high heat ensures consistent bonding and reduces the risk of defects caused by uneven temperature distribution. This makes silicone membranes an excellent choice for high-performance applications where precision is key.
3. Durability for Long-Term Performance
Silicone membranes are known for their durability and ability to withstand repetitive use without tearing or degrading the materials. Unlike traditional options, which can wear out quickly, silicone membranes maintain performance over time, reducing the need for frequent replacements.
This translates to cost savings and less downtime for manufacturers, making silicone membranes a reliable choice for glass lamination processes where consistent results are important.
4. Enhanced Optical Clarity
In glass lamination, optical clarity is a top priority, especially for applications like architectural glass or automotive windshields. Defects such as air bubbles or uneven interlayer bonding can compromise clarity and affect the overall appearance of the glass.
Silicone membranes play a crucial role in enhancing optical clarity by ensuring that the bonding process is smooth and free of imperfections. Their ability to provide consistent pressure and heat application minimizes the risk of visual distortions, resulting in crystal-clear laminated glass.
5. Versatility Across Applications
Silicone membranes are incredibly versatile, accommodating a wide range of glass lamination applications. Whether laminating flat glass, curved glass, or intricate designs, silicone membranes adapt to the shape and size of the workpiece. This flexibility allows manufacturers to use the same silicone membrane across multiple projects, increasing efficiency and reducing material waste.
Why Choose Silicone Membranes Over Traditional Materials?
While traditional materials like latex or polyurethane have been used in glass lamination, they fall short in several critical areas. Silicone membranes outperform traditional options due to their superior heat resistance, flexibility, and durability. They also provide better long-term value by reducing maintenance and replacement costs.
Here are the key advantages of silicone membranes over traditional materials:
- Lifespan: Silicone membranes last significantly longer, reducing downtime and costs associated with replacements.
- Heat Resistance: Silicone membranes can withstand extreme temperatures without losing performance, making them suitable for demanding applications.
- Flexibility: Their elasticity ensures even pressure distribution, eliminating defects and improving overall quality.
- Chemical Resistance: Silicone membranes are resistant to oils, adhesives, and other chemicals, maintaining their performance over time.
Elevating Glass Lamination with Silicone Membranes
Silicone membranes have set a new standard for glass lamination quality, offering unmatched performance, durability, and versatility. By providing uniform pressure, consistent heat resistance, and enhanced clarity, silicone membranes help manufacturers produce laminated glass that meets the highest industry standards.
For businesses looking to improve their glass lamination process, investing in high-quality silicone membranes is a smart choice. Smartech’s silicone membranes can transform your manufacturing operations and deliver superior results!
Looking for More Information?
Check out our Resources or Contact Us