Carbon Fiber Manufacturing Process Explained Step by Step
Carbon fiber, often called the “wonder material” of the modern age, has revolutionized countless industries, from aerospace to sports equipment. Its unmatched strength-to-weight ratio, combined with its flexibility, makes it the material of choice for various applications. The question is, how is carbon fiber manufactured?
The carbon fiber production process is an intricate dance of chemistry and engineering. Join us as we explain the carbon fiber manufacturing process, breaking it down step-by-step to provide a clear understanding of its making.
The Birth of Carbon Fiber: Key Ingredients and Precursors
At the heart of carbon fiber lies its raw materials and precursors. The quality and processing of these materials dictate the properties of the final carbon fiber. The primary precursor for most carbon fibers is a polymer known as polyacrylonitrile (PAN). Other precursors like rayon or petroleum pitch are also used, but PAN-based carbon fibers dominate the market due to their superior end properties.
Breaking Down The Carbon Fiber Processing Steps
Delving into the carbon fiber fabrication process, one discovers a series of carefully controlled stages, each contributing to the fiber’s distinctive characteristics. From the initial polymer processing to the final surface treatments, every step matters. Here’s a closer look:
1. Polyacrylonitrile (PAN) Processing: The Base Material
PAN is not just chosen randomly; it possesses specific characteristics making it ideal for carbon fiber production. Starting as a liquid polymer, PAN is spun into fibers, which undergo a series of treatments. This process ensures the PAN fibers have the required molecular alignment, setting the stage for the subsequent carbon fiber production steps.\
2. Stabilization: Preparing for Carbonization
Before carbon fibers can be born, the PAN fibers need to be stabilized. This involves heating the fibers in the presence of oxygen. The process allows for the fibers to oxidize, which stabilizes their molecular structure and prepares them for the intense heat they’ll face in the carbonization stage. Without this stabilization, the fibers wouldn’t survive the next process, or they’d produce an inferior quality carbon fiber.
3. Carbonization
At this juncture, the stabilized fibers are exposed to very high temperatures in an oxygen-free environment. This process ensures that all non-carbon atoms are expelled from the PAN fibers, leaving behind a fiber composed almost entirely of carbon atoms. The result? A material that boasts incredible strength and stiffness – the carbon fiber we know and admire.
4. Surface Treatment and Sizing
Freshly carbonized fibers have a surface that’s not entirely compatible with certain resins and bonding agents used in composite materials. This is where surface treatment comes into play. The carbon fibers’ bond compatibility with various resins improves by slightly oxidizing the fiber’s surface or etching it with certain chemicals. After this treatment, a protective layer, or “size”, is applied to the fibers to protect them and enhance their handling characteristics. This ensures that the carbon fibers are ready to be woven into fabrics or used in various applications without any compromise on their inherent properties.
The Carbon Fiber Lamination Process
When we speak of the strength and versatility of carbon fiber components, a significant part of that prowess stems from the carbon fiber lamination process. Lamination is the act of layering sheets of carbon fiber and resin to create a composite material that boasts properties greater than the sum of its individual layers. This method not only improves the structural integrity of the end product but also allows for a customizable approach, tailoring the laminate’s thickness and orientation to specific application needs.
It’s this meticulous layering and curing process that ensures carbon fiber components can endure the demanding conditions they’re often subjected to.
Carbon Fiber Parts Manufacturing
The final stage of the carbon fiber journey is its transformation into specialized parts that find their way into countless applications across industries. This endpoint, called carbon fiber parts manufacturing, is a synthesis of art and engineering.
Complex Molding for Custom Parts: Once carbon fiber sheets or threads are ready, they need to be molded into specific shapes to form parts. This often involves complex molds and procedures like compression molding and injection molding. These techniques require extreme precision; even the slightest miscalculation can compromise a component’s structural integrity.
The Role of Resins: An often underappreciated aspect of carbon fiber parts manufacturing is the resin used to bond the carbon fiber layers together. The type of resin impacts the part’s durability, weight, and resistance to factors such as heat or chemical exposure. Epoxy resins are commonly used, but others like polyester, vinyl ester, or thermoplastic resins are chosen based on the part’s end-use requirements.
Cutting and Finishing: After the molding process and initial curing, the parts often require cutting and finishing. This could involve water jet cutting, CNC machining, and various manual finishing techniques to ensure parts meet exact specifications. The finishing might also include painting, sealing, or the application of UV protective coatings, particularly if the parts are meant for exterior use.
Quality Control: Given that carbon fiber components are often used in critical applications — such as aerospace, automotive, and medical technology — quality control is paramount. This involves non-destructive testing methods like ultrasonic imaging or X-rays to detect any internal inconsistencies or flaws.
Sustainability Considerations: With the growing emphasis on environmental sustainability, carbon fiber parts manufacturing is also seeing an evolution. Techniques to recycle carbon fiber composites or repurpose offcuts are being developed. Though in nascent stages, these practices are integral for sustainable carbon fiber parts manufacturing.
The Smartech Advantage: Leading the Charge in Composite Solutions
Carbon fiber stands out in the material world, renowned for its extraordinary strength, lightweight properties, and exceptional durability. These attributes, however, can only shine when the manufacturing process integrates top-quality materials and technology — this is where Smartech makes a profound difference.
As an industry leader, Smartech takes pride in advancing the composite industry with its high-grade Reusable Bagging Sheets. Integral to the carbon fiber fabrication process, these sheets play a pivotal role in vacuum bagging applications. This method, crucial in the creation of strong, lightweight composites, requires a reliable and effective bagging sheet to ensure optimal results, and Smartech’s solutions are designed to meet these precise needs.
By choosing Smartech’s Reusable Bagging Sheets, you’re investing in reliability and the success of your carbon fiber fabrication. It’s not just about having the best fibers; it’s about complementing them with the best supplementary materials.
Ready to embrace excellence in composite production? Contact Smartech today,
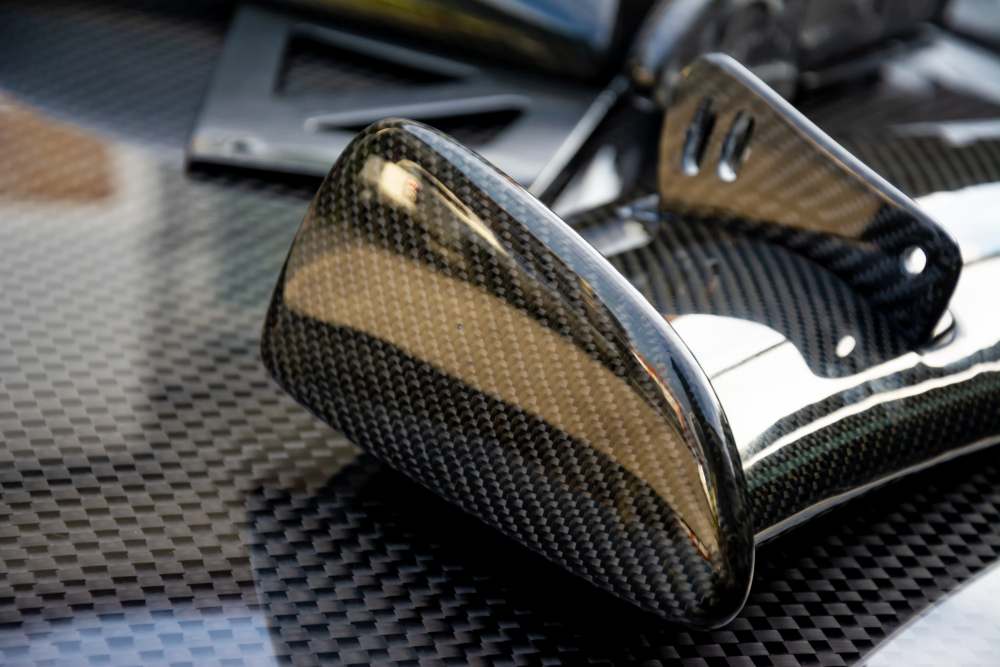
Looking for More Information?
Check out our Resources or Contact Us