Tips for Ensuring Employees’ Safety with Woodworking Laminates
Handling any machine part or manufacturing process carries a certain amount of risk to employee safety. This is true whether you operate an industrial level laminating press or a small woodworking shop.
Advances in equipment design, technology and stricter standards have led to improvements in safety for employees processing woodworking laminate. Still, OSHA standards for machinery and machine guarding were among the top ten most frequently cited violations in 2014.
Common injuries sustained while using industrial equipment include skin burns, inhaling fumes and getting limbs caught or smashed in machines.
Slips, trips and falls are also common in manufacturing facilities.
Keeping your employees safe and your company in regulatory compliance are both high priorities for your business.
Here are some tips for ensuring employees’ safety with woodworking laminates.
Woodworking Laminate Safety Tips
The goal is to prevent employees’ hands, arms and other body part from coming into contact with dangerous moving parts of laminating machines.
Take care with how you position equipment. For example, you want to position the operator’s control station at a safe distance from the laminating machine.
Use enclosure walls, fences and gates to keep employees out of areas with dangerous equipment.
Use machine guarding safety devices to block access to moving parts while laminating machines are in operation.
Use lockout/tagout procedures prior to servicing and maintenance. These procedures ensure that equipment is properly turned off and not powered up again until servicing or maintenance work is completed. This includes when laminating machines are being cleaned.
Keep the area around woodworking laminating machines free of tools and equipment, ladders, debris and liquid to reduce the chances of slips, trips and falls.
Make sure your production facility has proper and functioning ventilation and exhaust systems to prevent harmful fumes from building up in work areas and being inhaled by employees.
Use clear, concise warning and danger signs to bring attention to potential safety hazards. Place them in highly visible locations to keep them top of mind with employees.
What Is Basic Safety Training for Woodworking Laminate Staff?
Instruct employees to keep their limbs and clothing away from conveyor belts, rollers and feeders.
Train employees how to install laminate, and feed laminate and wood through the machine. Keep a record of who has been trained so untrained staff are not handling equipment.
Train employees to properly wear safety gear. Personal protective gear includes eye goggles, heat-resistant gloves, respirators, hard hats, safety vests and hearing protection devices.
Train employees how to identify safety hazards. They should also know how to report safety issues and respond to emergency situations.
Make sure employees are formally trained to operate support equipment like forklifts and pallet jacks before allowing them to use them.
Implementing and maintaining a strict safety regimen is essential for protecting employees handling woodworking laminating equipment.
Taking active measures to keep employees out of harm’s way safeguards your most valuable assets: your staff and your production line.
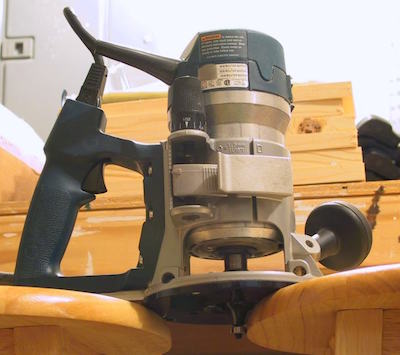
Looking for More Information?
Check out our Resources or Contact Us