A Guide on Choosing the Right Silicone Membrane Hardness
Silicone is a versatile material used in multiple industries, from medical tubing to seals in airplanes. Different types of silicone have varying hardness levels that determine their ideal use— you only want your material to squish when it should, after all. Hardness is one of the most important properties to consider when purchasing any of our wide range of silicone materials.
So, what makes the hardness of silicone such an important factor, how can you measure such a thing, and which hardness levels are best for which applications?
Before getting into why it’s so important to know the hardness of your silicone membrane, it’s best to familiarize yourself with the Shore Hardness scales. The Shore Hardness scales, invented by Albert Ferdinand Shore, along with his eponymous Shore durometer in the 1920s, is the primary scale and tool by which silicone’s hardness is measured and graded. It was invented—and still primarily used—for measuring the hardness of polymers, elastomers, and rubbers. However, it has also recently been used in the medical field for testing the properties of the skin. Shore Hardness can also be referred to as Shore durometer, sharing a name with the tool used to measure it.
There are twelve different scales, and each one uses a different durometer as a measuring tool. These scales are: A, B, C, D, DO, E, M, O, OO, OOO, OOO-S, and R. However, when it comes to measuring silicone, you will typically only see the Shore A Hardness scale in use.
Occasionally, you may also see the Shore D Hardness and Shore OO Hardness scales being used, but only if the material is incredibly hard or soft, respectfully.
Shore A Hardness
As with all of the Shore Hardness scales, the Shore A Hardness scale goes from 0A to 100A, with the material getting harder the further up the scale you step. On the extreme ends, they may also overlap with the aforementioned D and OO scales. Each silicone durometer has its own array of potential uses.
For instance, Shore 0A durometer is incredibly soft—comparable to a gel orthotic insert in its softness and consistency. It is best used to make molds that require intricate details to be replicated, as it has enough give to peel away from even small bumps and thin extensions without snapping them. On the other end, Shore 100A durometer often doesn’t even apply to silicone anymore but rather to harder materials like the polyurethane wheels of a shopping cart.
It should also be noted that the silicone’s durometer is only a measure of its hardness and not of other factors such as how quickly it will wear down or how resistant it is to impact or abrasion.
How It’s Measured
As mentioned before, the Shore Hardness of an object or material is measured with a Shore durometer. Each scale has its own durometer, and how the durometer looks can vary depending on how old it is and if it uses a digital or analog readout. However, they all have two key features shared between all of them: a circular readout at the top and a small metal pad with an even smaller metal cone at the bottom. In Shore A durometers, this cone is truncated, or flattened at the tip.
Once you have your workspace clean and ready, you simply have to take the durometer, turn it on if it has a digital component, then press it into the center of your material until it is completely flush and firmly pressed into the surface of the material. Then, simply write down the measurement displayed and repeat the process five more times in slightly different locations—still remaining close to the center—to get an accurate average measurement. You shouldn’t press so hard that you pierce the material, as you’re only checking for how resistant the material is to deforming when using Shore A.
Once you get into the middle of the Shore A Hardness scale, you start seeing many commonly-used silicone products. For instance, if you’re the crafty type, you may have used silicone stamps. These typically have a Shore Hardness of 40A-45A. Those cheap silicone wristbands often mass-produced for special events tend to be around 30A. If you want a good silicone watch band, it may be around 70A. Beyond that, these are merely consumer examples. More often than not, the most important and most prolific uses of silicone in your life are in places where you can’t see them.
To reiterate the introduction: you want your material to squish when it should. As demonstrated by its wide array of uses, silicone helps create many interesting products. However, apart from consumer dissatisfaction, there aren’t exactly high stakes at hand in the event that your silicone watch band snaps due to being too inflexible. So, what exactly is it that makes the silicone durometer such a pressing matter?
Silicone is used most in less glamorous places. Consider how a doctor may need to intubate your lungs in order to keep them inflated after a collapse. If this occurs, you would want that silicone tubing to be sturdy enough to withstand the pressure of your body without deforming or collapsing.
Similarly, if you’re flying in a plane, you’re essentially sealed in a pressurized tube tens of thousands of feet in the air. Understandably, you would want all of the seals in the fuselage to be able to deform and adjust to the differences in air pressure as smoothly as possible to avoid air leaks and depressurization. These are just two of many applications in which choosing the right silicone hardness can be a legitimate matter of life or death.
Whether you’re casting an incredibly intricate mold or saving the life of an intubated patient, choosing the right hardness for your silicone is the first step toward success. This also applies to our wide range of silicone membranes, which Steinbach designed for use in woodworking 3D lamination, composite forming and infusion, solar panel manufacture, and glass lamination. These applications are also reliant on the Shore Hardness of our silicone membranes being in a fine balance. Using the 3D lamination as an example, if the silicone is too soft, it may not provide the proper forming pressure during lamination and is more sensitive to tearing. Conversely, if the membrane is too hard, the end product may lose detail since the membrane won’t be able to deform enough to press into tight contours. Beyond that, hard silicone is also at a higher risk of fracture due to inflexibility.
No silicone hardness is better or worse than any other. Rather, they all just have different applications. Whether you’re building as a hobby or doing practical engineering on a salary, it is ultimately your responsibility to make sure your tools match your job.
Warning: Illegal string offset 'title' in /nas/content/live/smarttechint/wp-content/themes/smartech/layouts/side_by_side_content_image_video.php on line 30
Notice: Uninitialized string offset: 0 in /nas/content/live/smarttechint/wp-content/themes/smartech/layouts/side_by_side_content_image_video.php on line 30
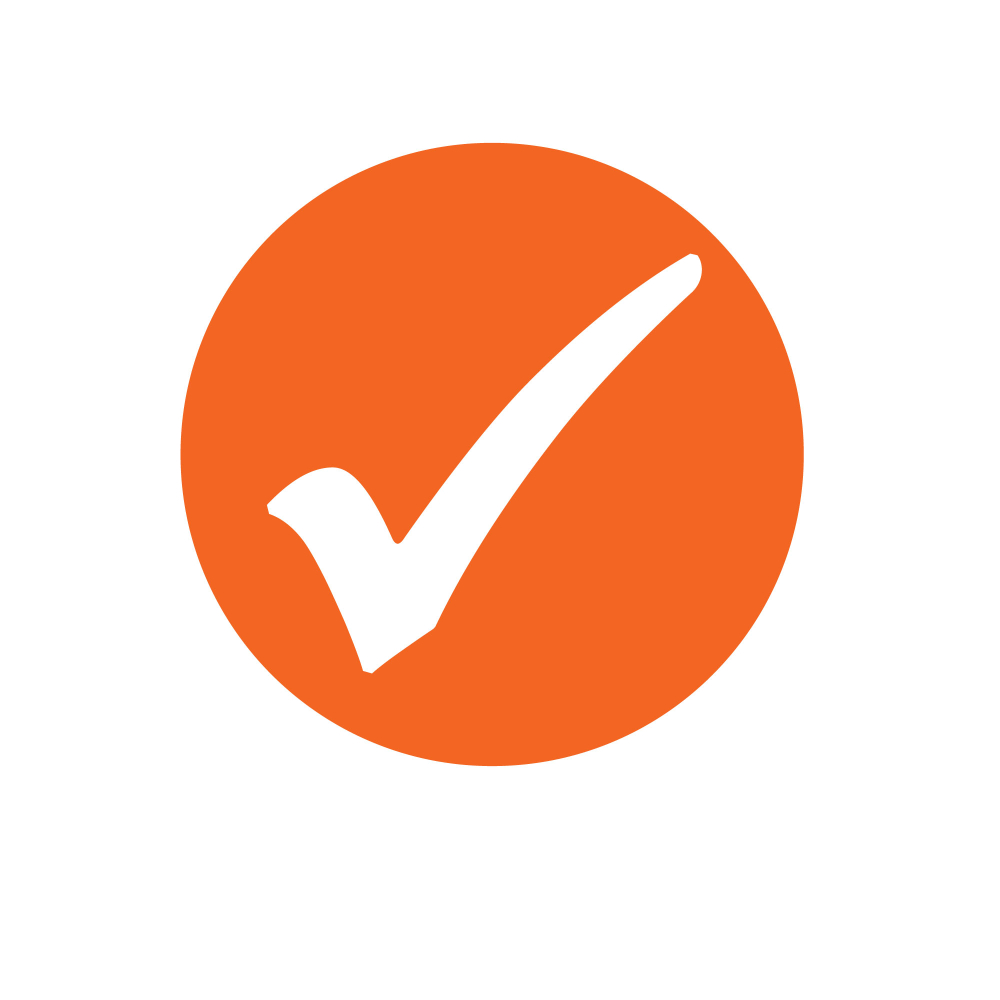
Looking for More Information?
Check out our Resources or Contact Us