3D Printed Ceramic Applications & Advantages
The 3D printed ceramic parts created by Smartech/Steinbach are made from aluminum oxide or zirconia oxide mixed with a polymer to transform the powder particles it into a slurry. A special type of 3D printer prints the slurry material into a specific pattern, layer by layer, until the final object is formed. This printing process allows for the creation of complex shapes and designs that may be difficult or even impossible to produce using traditional ceramic manufacturing techniques such as casting, pressing, and extrusion.
After the ceramic parts have been printed, they go into the de-binding furnace, the binder (embedded photopolymer) is thermally decomposed and degassed from the green body. When the de-binding has been completed the parts will go into a sintering furnace, the parts are heated up to 1,650°C. This bonds the powder particles, resulting in the molded part to become compacted and solidified. Sintering produces a dense part with a smooth surface. The thermal treatment results in a linear shrinkage of approx. 30%. It is the combination of the software, material, printer and last but certainly not least, the skills of the technicians that results in the high level of precision that can be achieved. The achievable tolerances are in the range of approx. +/- 0.1 mm or +/- 1%. Closer tolerances down to max. ±0.05mm might be possible after several iterations.
What Are 3D Printed Ceramics Used For?
3D printed ceramics are an innovative technology as they represent a significant advancement in the field of ceramic manufacturing. Traditionally, ceramics have been produced using techniques such as casting, pressing, and extrusion, which are limited due to the complexity of shapes and designs that can be created. 3D printing technology, on the other hand, allows for the creation of complex, three-dimensional shapes and designs with high precision and accuracy. This opens up new possibilities for 3D printed ceramic components, which allows for the creation of custom and highly detailed objects that may not be possible only using traditional techniques. Overall, the combination of design flexibility, precision, and material properties offered 3D printed technical ceramics makes it a highly innovative technology that has the potential to transform the field of ceramic manufacturing.
Applications of 3D Printing Ceramics
3D printed ceramics have a wide range of potential uses across industries. Common 3D
printed ceramics can include: Medical technology, Automobile industry, Analysis and measurement equipment, Microreactors / Microfluidic applications, Micro-electronics, Plasma technology, Aerospace sector and Chemistry and laboratories
Aerospace & Automotive Industries
3D printed ceramics can be used to create lightweight, high-strength parts for use in aerospace and automotive applications. Ceramic materials are particularly well-suited for use in these industries due to their high-temperature resistance and ability to withstand harsh environments.
Electronics
3D printed ceramics can be used to create components for electronic devices, including sensors and circuit boards. Ceramic materials are often used in these applications due to their high thermal and electrical insulation properties.
Energy
3D printed ceramics have revolutionized the energy industry by enabling the creation of custom components for use in both power generation and storage. Ceramic materials are often used in these applications because of their high-temperature resistance and ability to withstand harsh environments.
Medical & Dental Applications
3D printed ceramics can also be used to create custom prosthetics, implants, and other medical devices. Ceramic materials are often used in these applications due to their biocompatibility, durability, and resistance to corrosion.
Prototyping
3D objects are often used in prototyping and product design to test out and refine new designs before manufacturing.
When to choose for Ceramic instead of plastic?
Plastic (polymer) parts will fail where ceramic parts will thrive in application when they are required to be heat-resistant up to 1600°C/2900°F, non-conductive, wear-resistant and need to have a smooth surface, be biocompatible, solid, food safe and chemically resistant.
Advantages of 3D Printed Ceramics
The advantages of 3D printed ceramics make it a promising technology for a wide range of applications and industries. Here are some of the benefits you can expect with 3D printing ceramics.
Heat Resistance
Ceramics can withstand high temperatures, making them suitable for use in many high-temperature applications or situations where fluctuations in temperature can be expected.
Strength & Durability
3D printing ceramic materials are inherently strong and durable, which makes them ideal for use in applications that require high resistance to wear and tear.
Precision & Accuracy
3D printing allows for more precise control over the ceramic material, which results in highly accurate and uniform parts. This can lead to improved product quality and consistency overall.
Design Flexibility
3D printing allows for the creation of complex specifications and intricate designs that are not possible with traditional ceramic manufacturing techniques. This allows for greater design flexibility and customization, as well as the ability to create unique, one-of-a-kind objects.
Customization
3D printing allows for easy customization of ceramic parts, making it possible to produce unique parts for specific applications or customers.
Reduced Lead Time
3D printing can significantly reduce lead time, which can result in efficient production and delivery of ceramic parts.
Reduced Waste
Traditional ceramic manufacturing techniques often result in a significant amount of waste due to the need for molds and other tools. 3D printing eliminates the need for these tools, which ends up reducing overall waste while also increasing efficiency.
Cost-Effective prototyping
3D printing is often used for creating prototype parts. Traditional manufacturing processes often require the creation of expensive molds or tooling. With 3D printing, however, the need for such molds or tooling is eliminated, which results in lower production costs for especially small-scale production runs.
The absence of tools also means that it is easy to adjust the design by just changing the STEP.file. This flexibility and the absence of significant costs for changes make it perfect for prototypes
3D Printed Ceramics with Smartech
Smartech has partnered with Steinbach to offer its innovative 3D printing technology used to create a variety of ceramic parts with a wide range of applications. These highlighted advantages make 3D printed ceramics useful in a wide range of applications across various industries, from aerospace and automotive to medical and electronics. Explore 3D printed ceramics with Smartech and speak with one of our representatives to find the best solution for your next project.
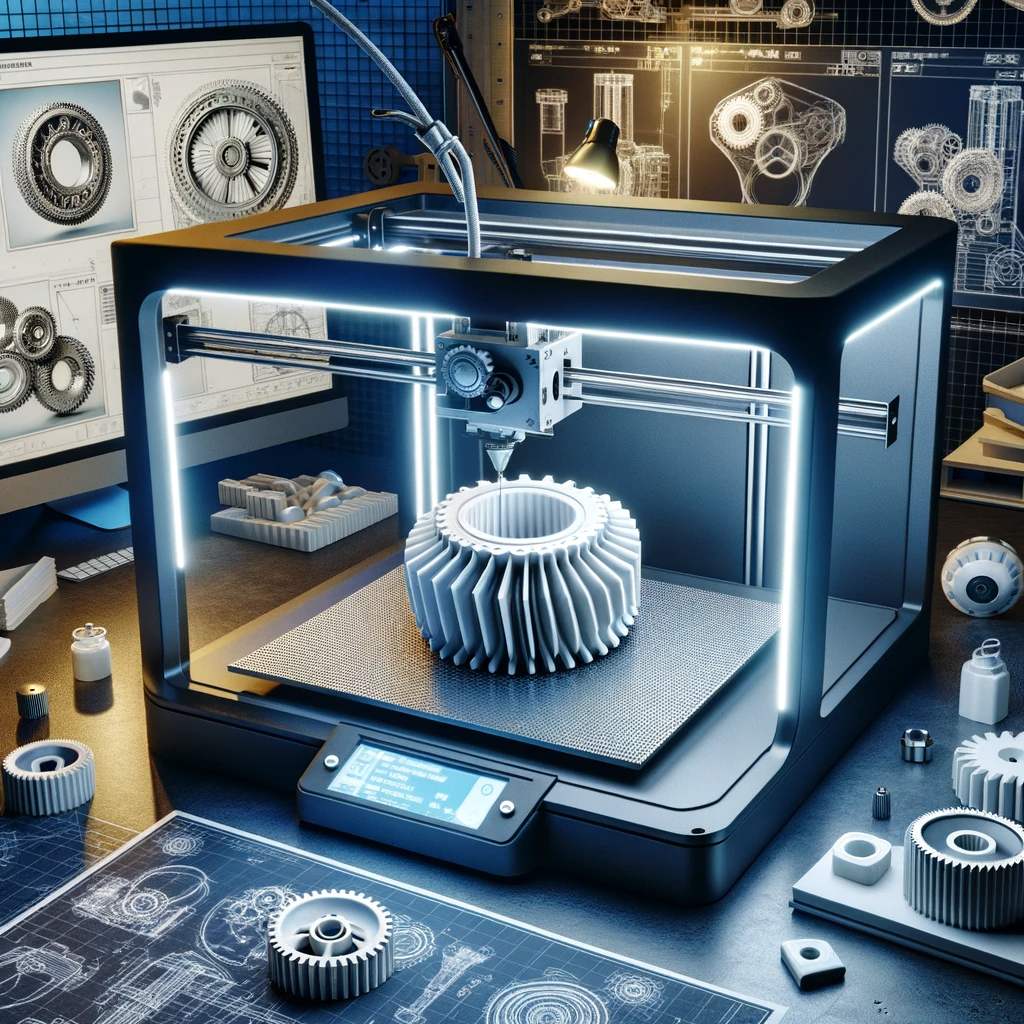
Looking for More Information?
Check out our Resources or Contact Us